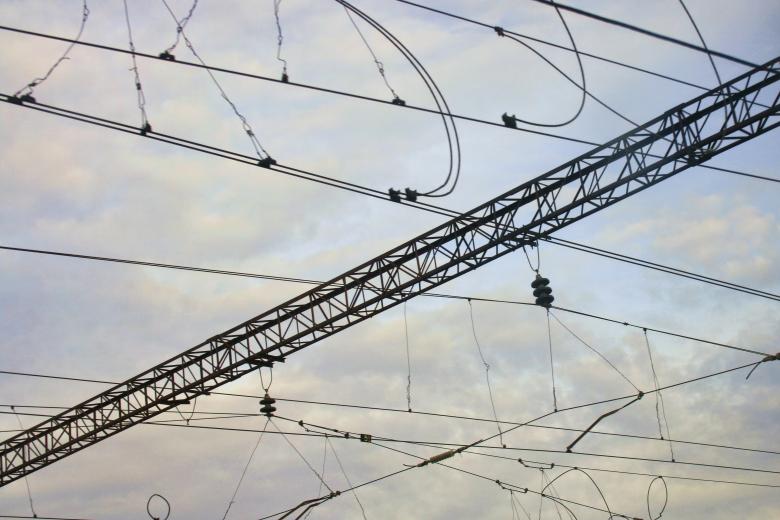
CPS Energy depends on a variety of goods and services to provide Safe, Reliable, Affordable and Resilient energy to customers throughout Greater San Antonio. Recent material shortages across the globe are impacting supply chains that provide those goods and services.
The coronavirus pandemic, labor shortages, and other events have caused major production interruptions for many manufacturers at an international scale. Current demand for products and supplies are dramatically exceeding the available supply, which is putting a strain on supplies that CPS Energy and other utilities use daily. Supply shortages are expected to continue through the fall of this year and may extend into 2022.
An increasing list of raw materials is causing challenges for manufacturing. This includes:
- Ethylene Resin (Manufacturing of polymers such as polyvinyl chloride or PVC)
- Vinyl Acetate Monomer (Adhesives, water-based paints, nonwoven textile fibers and more)
- Lumber
- Semiconductor Chips (Electronics)
- Solar Glass and Wafers (Solar Panels)
- Butadiene (Synthetic rubbers such as tires, plastic gloves, rubber hoses)
- Styrene (Latex, Synthetic rubbers and polystyrene resins)
CPS Energy is working diligently to minimize the impact of material supply shortages. Currently, lumber products, products that contain resin such as polyvinyl chloride (PVC) electrical conduit, and certain metals like those contained in meter sockets are becoming scarce. Additionally, the utility is experiencing challenges in acquiring transformers—an essential piece of equipment required to deliver electricity to homes. These material shortages are likely to impact CPS Energy’s support of outage restoration and new construction efforts. It’s important to keep in mind that all electric utilities are experiencing these shortages on a global scale.
CPS Energy is taking a highly creative approach to the materials shortage challenges. The utility has already begun discussions with local manufacturers on the possibility of manufacturing materials, such as meter sockets, to help alleviate the shortage. The ability to think globally and act locally is a common practice for CPS Energy, and these discussions serve as an innovative step in managing the impact.
“Storm restoration disruption and delaying customers’ projects is something our supply chain team is working very hard to avoid,” said Maria Garcia, CPS Energy’s Vice President of Supply Chain. “These supply constraints are not unique to our community. Our peer utilities across the country are taking similar actions to ours such as diversifying their specifications and suppliers to allow for greater flexibility in procuring these critical items, without sacrificing product safety, resiliency and reliability.”
Developers and other potentially impacted customers are asked to plan for potential delays caused by material shortages in their active and upcoming construction and renovation projects. Additionally, CPS Energy is seeing rapidly rising material costs that are associated with the shortages, and ask impacted customers to consider the potential for rising construction costs when planning their projects.
If you are a developer or contractor you will see the latest updates to this global materials shortage when you log into the CPS Energy system to check on your projects. CPS Energy will continue to keep a steady flow of communication with our customers and stakeholders as one of our highest priorities.
For more information, please visit cpsenergy.com.
Source: CPS Energy