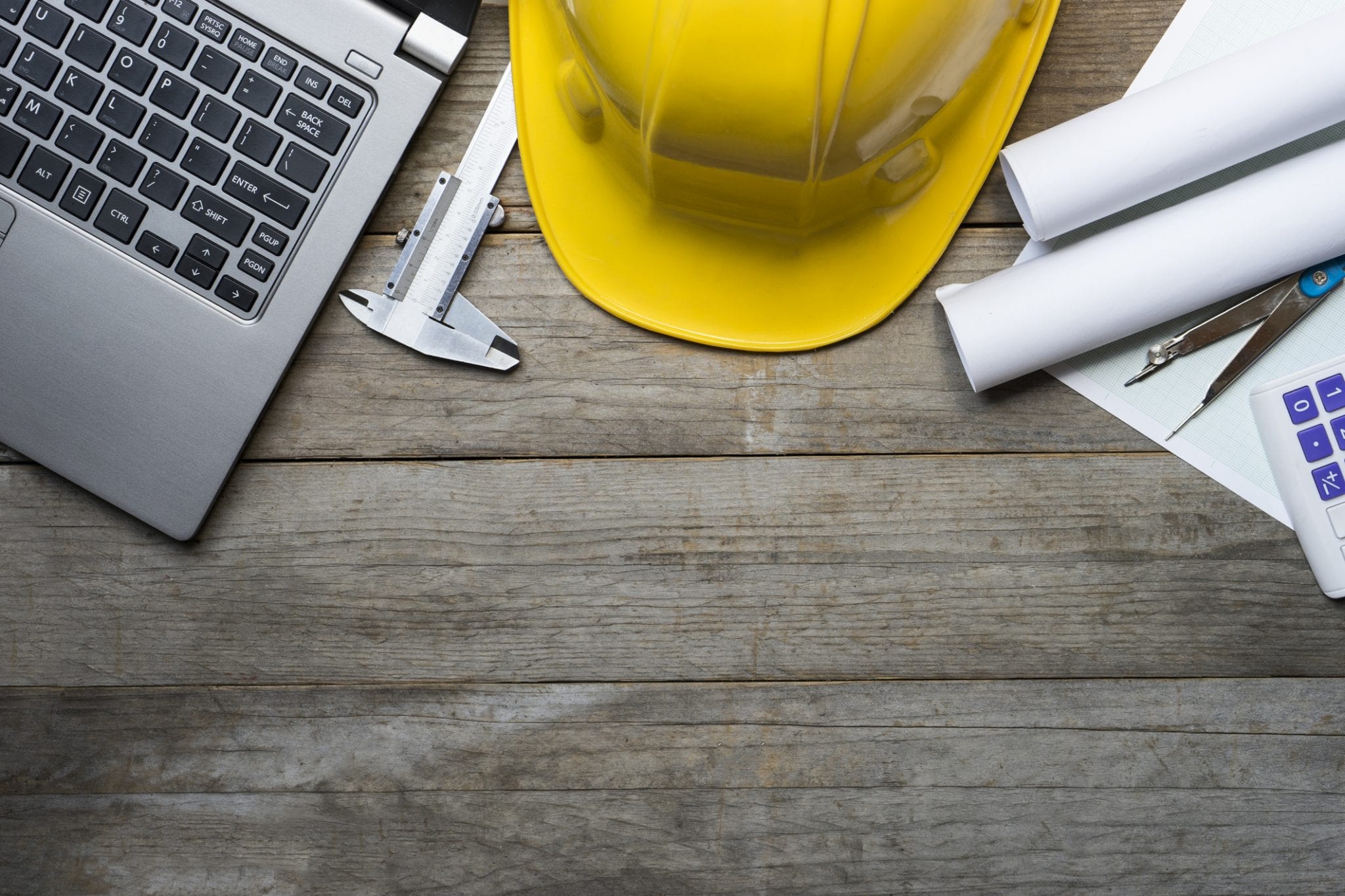
Construction jobsites will one day be bustling with “terminator-type,” humanoid robots, according to Scott Peters, president and co-founder of Construction Robotics, but that future may be a long ways off for the industry.
For now, the Victor, New York-based company recognizes that human workers have unique expertise and problem-solving skills to offer, and that to increase productivity on jobsites, robots should first be used to augment those capabilities.
“Humans have this amazing ability to take a challenging situation, think in real time and then be able to adjust to it,” he said in a recent webinar titled Robotic Construction: How Much, How Soon and What’s First. “How do we take that unique human capacity and leverage that in the best way that we can?” he questioned.
Over the past several decades, the manufacturing industry has seen employment stagnancy and declines the likes of which the construction industry experienced after the Great Recession. But unlike construction, manufacturing has pulled off a productivity boom, Peters said, in large part thanks to automation of repetitive tasks and amplification of the work that humans are doing.
Construction Robotics adopted this strategy with its semi-automated mason, or SAM, which is three to five times more productive than a human mason due to its ability to lay 250 to 400 bricks per hour compared to a typical mason’s 300 to 500 bricks per day, the company says. Still, it’s designed to work alongside other workers who can verify quality and own the finished product, Peters noted.
Where can robotics make inroads?
In its research and development, Construction Robotics targets similarly repetitive tasks on the jobsite, asking the question: “Where is someone doing the same thing over and over again where we can apply a robot to assist that person and either take the physical strain out of their work or increase the speed at which they’re able to work?”
The company released in January its Material Unit Lift Enhancer, or MULE, which takes on the weight of a large block while leaving it in the hands of a worker who can skillfully maneuver and place it without the strain.
“We can take an up to 135-pound unit, whether that’s a block, a stone panel, a veneer panel, […] and we can make it weightless with infinite dexterity and control,” Peters said. “As we take the weight off their shoulders, the weight off their back, we reduce injuries, we reduce fatigue and that allows other aspects of the work to be more successful.”
In one case, according to Peters, a company using the MULE said it was able to grout three times faster than without the robot, because workers had plenty of energy to spare once the blocks were laid. The MULE has versatile uses because it can be set on the ground, a scaffold or to a freestanding height of 20 feet, Peters said.
Still, robots are not a magic bullet and won’t eliminate challenges overnight, Peters noted. As is the case with any emerging technology, construction companies can’t expect to work it into their routine without some adjustments. “You need to take time, you need to properly invest and you need to really embrace that technology as a way of life because it is going to change our industry,” he said.
Source: Construction Dive