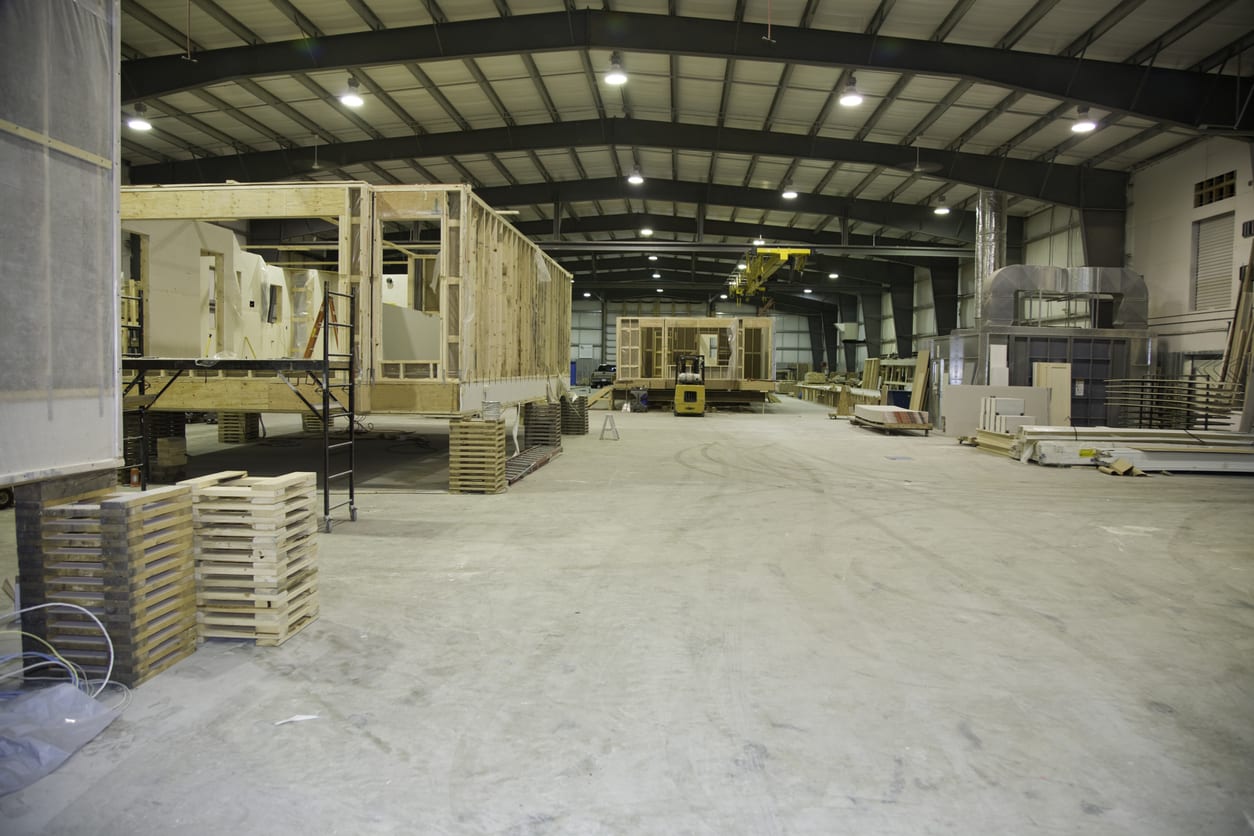
Modular construction is known for shaving time from construction schedules and reducing project budgets. But in the case of the $10 billion ExxonMobil-SABIC ethane steam cracker and plastics plant in Corpus Christi, Texas, it looks like it is also going to do away with some jobs as well.
After the two energy giants announced the project a few years ago and began planning, they amassed about $500 million in tax incentives from local communities with the promise of impressive economic benefits, including about 11,000 construction jobs, according to the Houston Chronicle.
But between the time that building begins in the upcoming quarter, through the anticipated completion date of sometime in 2022, the ExxonMobil-SABIC joint venture vehicle of Gulf Coast Growth Ventures expects that the project will actually deliver 6,000 construction jobs instead, due to a switch in approach to modular construction. The company has been making this downward-revised projection since at least May 2018.
An ExxonMobil spokesperson told the Chronicle that the JV made the choice because local residents had expressed concern about the effects of so many workers coming into the community. With the modular approach, there will be fewer workers, and the project can be completed faster, she added. The team of The Wood Group; McDermott & Turner Industries Group; Chiyoda & Kiewit; and Mitsubishi Heavy Industries & Zachry Group will be handling the engineering, procurement and construction phases.
Even with the lowered expectations, 6,000 jobs is enough to retain the original tax breaks, according to the Chronicle.
Although the industry is used to seeing modular construction for projects like hotels and apartment buildings, modular advocates say the method can be used on any type of construction project and considered modular as long as components are manufactured offsite and then those pieces assembled at the jobsite.
According to a recent report from McKinsey & Co., modular construction boosts productivity and could save new-build real estate projects in the U.S. and Europe a combined $22 billion annually by 2030. The method is able to save up to 50% on a project’s schedule when compared to one using traditional methods, and can shave up to 20% off the budget.
These benefits are more likely to be achieved, McKinsey said, if developers and contractors use the appropriate materials and design and can be innovative in overcoming the design, manufacturing, technological, logistical and assembly challenges that come along with such projects. They must also use locations where the project team can realize scale and repetition.
Source: Construction Dive