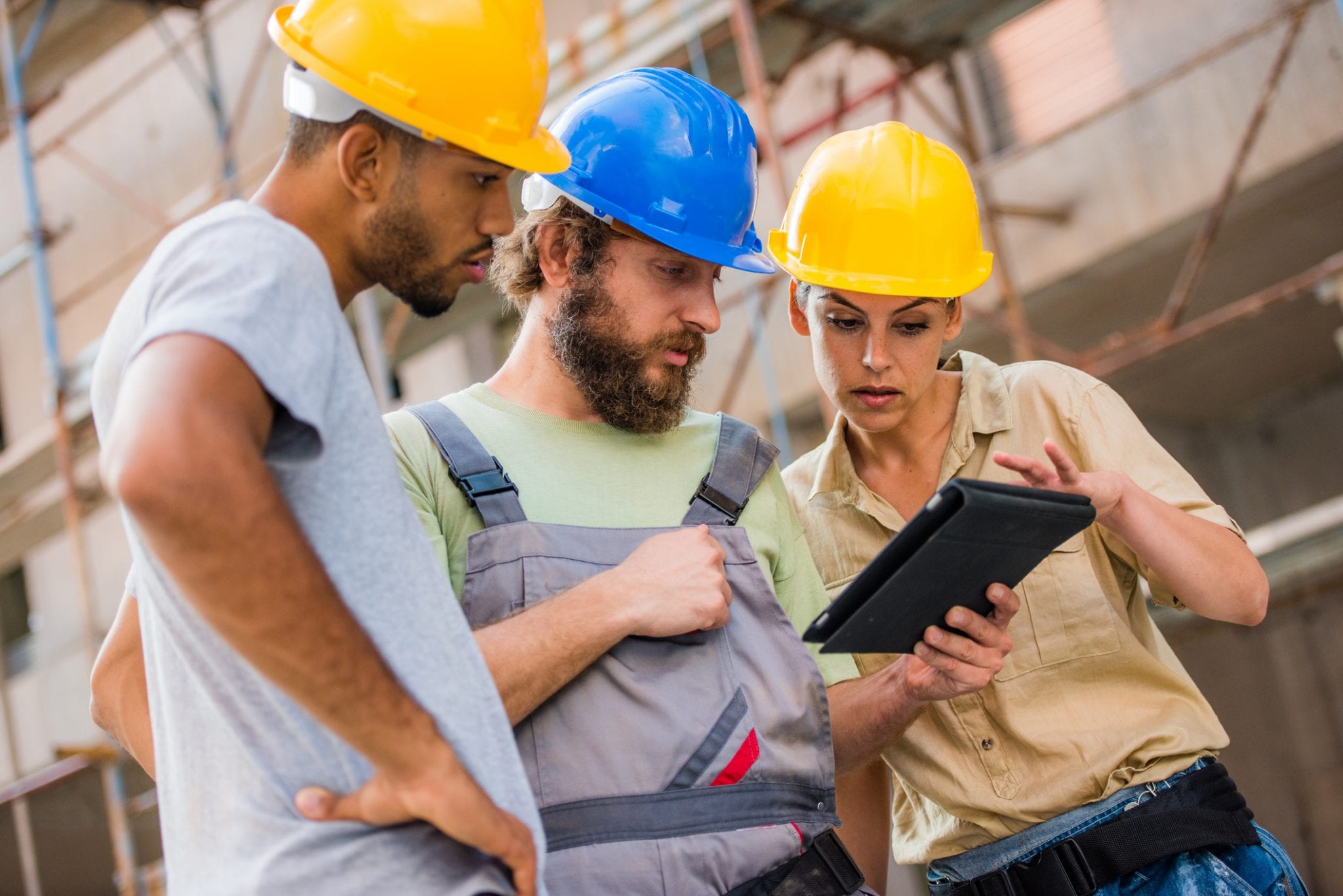
When McKinsey released a report in February 2017 about construction’s productivity gap, much attention was given to the industry’s abysmal 1% annual productivity growth rate, which is less than half of the 2.8% global construction growth rate. However, McKinsey’s report said U.S. contractors could increase productivity in part by “infusing digital technology, new materials and advanced automation.”
Construction Dive has been hearing a lot from industry leaders and tech companies about how technology is improving productivity and accuracy, so we asked readers, through a short survey and interviews, about the hardware they find most effective in the field. Here are the top devices contractors praised.
- Tablets and mobile devices
Nearly 93% of contractors use smartphones on the jobsite and about 65% use tablets, according to the 2018 JBKnowledge ConTech report. The survey indicated these items enable easy access to mobile applications that help streamline business, such as daily reporting and photo documentation apps.
Construction firms that responded to a recent Construction Dive survey shared myriad benefits of iPads:
mobility and flexibility
going paperless
easier print reading
easy access to drawings, daily reports, quality control inspections, safety audits, email
- Drones
The JBKnowledge ConTech survey also said about 57% of general contractor respondents use drones on the jobsites. Structr Advisors, a construction consulting firm in Richmond, Virginia, noted it uses a drone to record spatial location, distances, temperature, ambient and material humidity, as well as capture digital photos.
“For a relatively low cost, we can fly a drone over a site, compile a database of pictures and process those pictures to create a 3D site model,” said Jordan Olson, virtual design coordinator for Brasfield & Gorrie, based in Birmingham, Alabama. “We can then use that site model for a variety of purposes, such as project rendering, cut/fill analysis or simple owner communication.”
- Headsets
Whether they be augmented reality, virtual reality or mixed reality devices, headsets are proving to be invaluable tools for the industry. Skanska USA told Construction Dive it uses Microsoft HoloLens for design verification, quality assurance and quality control.
Jennifer Suerth, vice president of technical services at Chicago-based Pepper Construction, recently shared the value the HoloLens has brought to Pepper in the field. The firm has a division that pours concrete and prior to each pour, field technicians put on HoloLens headsets and walk the site to see a model of where elements are.
“[The technician] doesn’t need to look at drawings or specs or even have to measure,” she said. “He’s just seeing it. He can quickly inspect the slab in a way faster and higher quality time than he would have in the past.”
- Laser scanning
Referencing the company’s concrete pouring division again, Suerth explained how laser scanning expedites and improves operations. A pre-pour scan captures rebar and other elements while a post-pour scan allows workers to look at deflections to see the pour does not deviate from the design. In addition to improving the work quality, Suerth also said it gives the group an opportunity to leverage collected data downstream.
Boston-based Suffolk Construction told Construction Dive this month that it has introduced 3D laser scanners on jobsites in South Florida to flag any discrepancies between the design model and the reality onsite, in order to prevent construction errors and rework. An HVAC subcontractor for a Miami-area high-rise project, according to the company, was able to use the scans to ensure his diffusers would fit the tower design’s curving angles.
- Wearables
Although they have yet to make significant inroads in the industry — a Dodge Data & Analytics SmartMarket report last December found only 13% of firms use wearables — the contractors that adopt wearables by and large find them to be worth the investment. The same study found that of the 13% using the technology, 82% of those firms said wearables have had a positive impact with regard to improving safety in the field.
SangHyun Lee, an associate professor at the University of Michigan, is also studying how wearables can increase construction worker safety. A device as simple as a wristband can measure biometric figures like skin temperature, heart rate and electrical activity on skin to keep tabs on workers’ statuses and hopefully prevent accidents.
There are many possibilities for wearable technologies beyond wristbands, though. The Massachusetts Institute of Technology is developing a Safety++ suite of internet of things-enabled devices, including jackets that alert workers to harmful toxins and decibel levels and shoes that can sense if the wearer is carrying a dangerously heavy load.
Jack Moran, BIM services manager at Consigli Construction in the Boston area, told Construction Dive that his firm recently purchased exoskeleton suits. Those suits will take weight off workers in the field, he said, which will increase their safety and enable them to do a better job because they will experience less muscle fatigue.