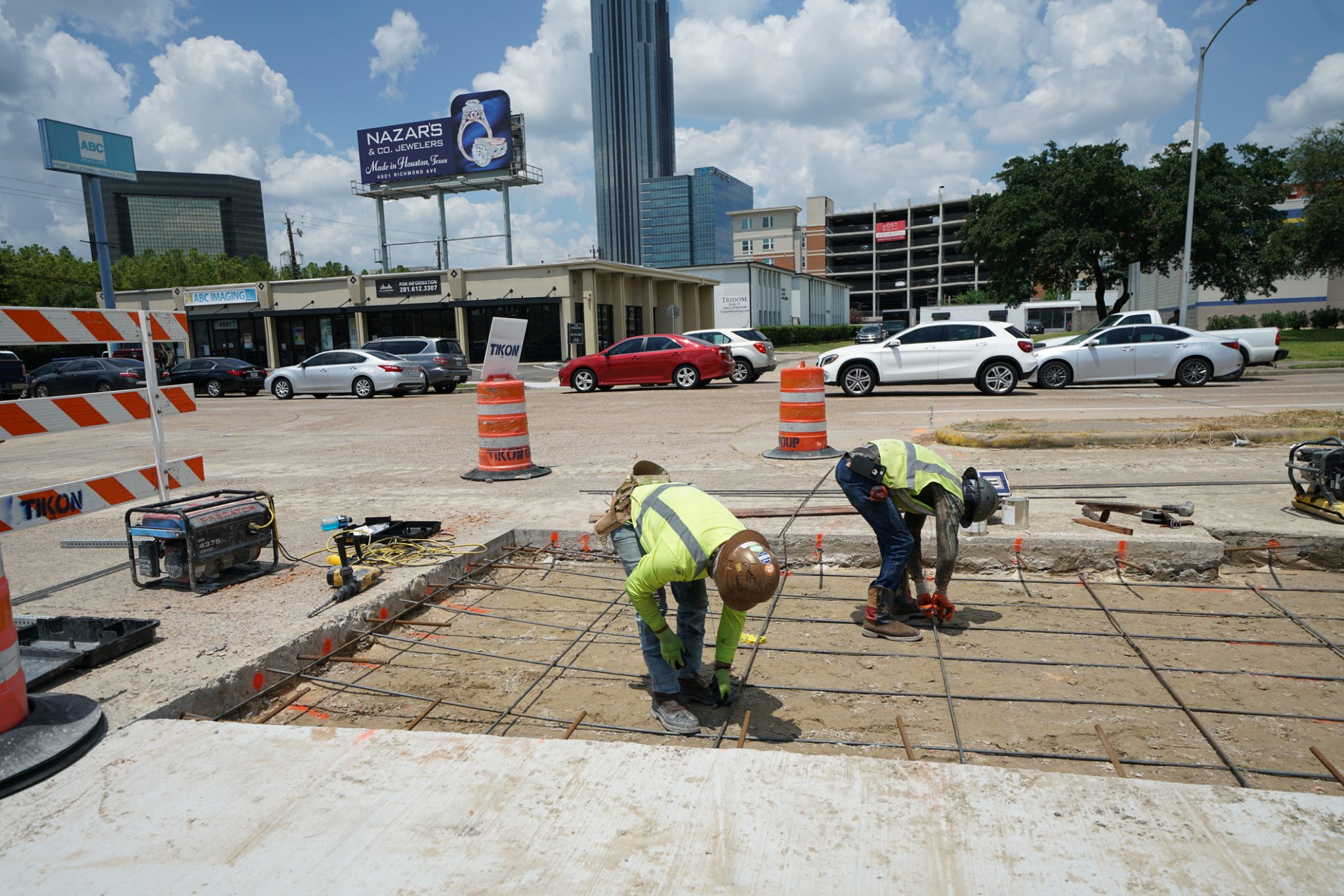
The coronavirus pandemic has shocked U.S. construction into needing to adopt new technologies to maintain social distancing and monitor jobsites remotely. Those adaptations, some construction leaders say, should have been adopted in the first place, before the pandemic forced contractors to implement them.
The outbreak has also forced more connection between the site and office, as most office workers have been relegated to working from home. Shared data and digital connectivity is becoming the norm, said Scott Crozier, general manager of civil engineering and construction for software company Trimble, as engineers, architects, site supervisors and other stakeholders need up-to-date information no matter the construction environment.
Not only has tech within companies been lacking, as often one worker with a single USB is in charge of distributing data on some sites, Crozier said, but government inspections requiring in-person, scheduled visits may mean project delays.
Crozier noted that inspectors are beginning to allow the use of technology for virtual inspections. In Europe, he said, often a contractor doing a specific job, such as laying pipe, will fully document the work and have it reviewed by remote inspectors, which speeds up the process immensely, because no one needs to physically visit the site.
A main reason why the U.S. construction industry is behind in tech adoption, Crozier said, is lower costs of labor. Cheaper labor, despite there being a lack of skilled workers, means less demand for tech. In Europe and Australia, he said, the higher cost of labor means contractors need to innovate, and rapidly. That combination often attracts young Americans with construction and tech backgrounds to those countries as well, as opposed to keeping these innovators in the U.S.
Recent implementations
As construction was deemed essential and allowed to continue in nearly all 50 states, contractors were required to follow CDC guidelines to protect workers from the spread of COVID-19. In response, tech firms and safety app developers introduced or expanded a variety of applications that some construction leaders say will become the norm.
Some applications use image data or wearables to track workers, ensure they maintain social distancing, or at the very least, reduce social density on jobsites. Other apps provide questionnaires for workers prior to allowing them onsite to ensure they were as low risk as possible for having and spreading COVID-19. Plus, others allow for virtual walkthroughs so stakeholders in their homes can have up-to-date imagery of work in progress.
“That’s what COVID and social distancing brought us, but that’s actually the right practice,” said Jon Fingland, general manager of collaborative solutions at Trimble.
Likewise, internet of things-based devices that track workers’ locations and allow the scheduling of specified work on certain days for more accurate measuring of productivity will be tomorrow’s “right lean practice,” Fingland told Construction Dive, meaning the best route to minimizing waste of materials, time and effort to maximize productivity and value.
Reducing the number of workers in a space can help protect them and reduce the spread of COVID-19, but, he said, that practice is essentially the same as scheduling workers for one section of a job at a time. For example, ensuring there are only 10 drywall workers on one day then five painters the following day allows for better monitoring of productivity.
No more status quo
New technologies being introduced are moving down from top management. During a webinar from the Society for Construction Solutions New York Chapter, Anita Woolley Nelson, chief strategy officer of Skanska USA Building, said several executives at the company are taking base training for tech practices to prepare for the future.
“While I believe contractors will continue to use scheduling technology in the future, the landscape will be different,” said Matt Abeles, vice president of construction technology and innovation for Associated Builders and Contractors (ABC). ”Using site monitoring technology will become more prevalent, so stakeholders not physically on the jobsite can have a transparent view on progress.”
Having stakeholders working remotely will aid in speeding up projects, Abeles said.
Perhaps the most basic integrations are the most unexpected, Abeles said. “One of the biggest surprises of all of this is the necessary adoption of collaborative technologies such as videoconferencing, which contractors are embracing more than ever in response to COVID-19,” he told Construction Dive.
Nelson also didn’t seem to think that things would return to the status quo when the pandemic ends. “People always say you can’t take a jobsite home with you, [but] maybe you can,” she said.
Source: Construction Dive